OSCA brings supply chain visibility to textile licensee
31st March 2022
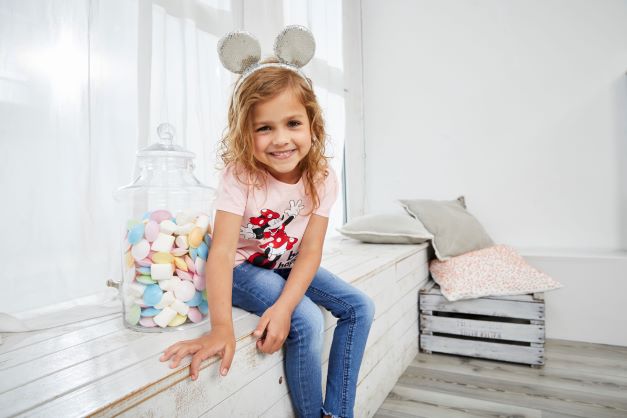
Whether it’s Superman, Batman or the Avengers: The German licensee of these motifs is relying on Setlog’s software OSCA to better manage its supply chain for the production and transportation of clothing with movie and comic motives.
The German marketing specialist for textiles and accessories of popular licensed brands signed a contract with Setlog at the end of 2021. With that, the company set the foundation to be up to date in terms of digitisation of supply chain management. Setlog’s OSCA SCM and OSCA CSR modules will go live at the end of the first quarter of 2022.
“With OSCA SCM, we can track our orders digitally via a transparent supply chain. We chose Setlog’s tool since it is the best solution in an international benchmark,” emphasises Holger Schmies, Managing Director and co-owner of the company. One of the reasons why the enterprise also uses OSCA CSR (Corporate Social Responsibility) is to be able to comply effortlessly with the regulations from future supply chain due diligence laws.
OSCA is easy to implement and makes it possible to quickly manage and control all supply chain processes. “The software replaces emails, Excel lists and last-minute calls about delivery changes,” explains Ralf Duester, board member of Setlog.
Whether Disney, Warner Bros, Marvel, Peanuts or Paw Patrol – the German licensee is holding licenses for popular comic and movie heroes. Textiles with prints of the characters are produced up to 85% in the Far East – the rest in Portugal and Turkey. In the future, the company will transmit all orders from its ERP system to its two dozen suppliers directly via Setlog’s software.
From order confirmation and delivery planning to transport bookings and shipments, the SCM software always serves as a central communication hub for all partners along the supply chain. With the software, the company can control costs, volumes, lead times, transport times and routing, carton packing lists (including label generation) as well as delivery dates.
The four logistics service providers the licensee works with will transfer transport notifications and tracking data directly into the Setlog platform to thus supporting a single point of access. For a digital data exchange of order and transport information with the TMS solutions of the forwarding companies, Setlog has developed a REST API interface. A KPI dashboard visualises the most important key figures for the employees.
All partners in the supply chain are informed simultaneously and in real-time as soon as delivery data changes or delays occur. Once OSCA goes live, all shipments will run through the system. For 2022, the company expects between 250 and 300 FCL container as well as LCL shipments to be centrally controlled and handled this way.
To easily comply with the regulations of future supply chain due diligence laws in the EU and Germany, the fast-growing company relies on the OSCA CSR solution. Within the system, the structures and tier levels of global supply chains are displayed transparently. New supply chain partners can easily be integrated into the system. Suppliers, agencies, factories and other upstream partners are added according to a standardised onboarding process.
“Due to our growth in sales, server space for certificates, email traffic and the work of the CSR department increased. With the help of OSCA CSR, we want to reduce these burdens and bring transparency to the processes,” explains Schmies.
The benefits of the solution include:
- Easy tracking of audits as well as certifications including an early warning system that strikes as soon as the validity of the documents expires.
- Violations of regulations can be classified and tracked in an uncomplicated manner.
- The regulations (e.g. the Code of Conduct) are clearly presented and can be distributed simultaneously to all partners involved in the respective process.
- Surveys to partners can be created and distributed quickly. The user can easily filter out unprocessed surveys.
Background
The topics of sustainability and certification are very important to the company. Some of the products are produced according to cradle-to-cradle principles. “Our suppliers completely disclose which materials are used for production and guarantee that no materials harmful to the health are used for this. The water for production comes from the company’s own water cycle and the electricity used comes from water or solar energy,” says Schmies.
In addition, the licensee manufactures textile products that are STANDARD 100 by Oeko certified. The company works in the Better Cotton Initiative, where farmers are trained to produce cotton in an environmental-friendly way, thereby increasing their income. The management is also committed to the Organic 100 Content Standard (OCS) and operates under the Global Organic Textile Standard (GOTS).
The enterprise is also part of the Amfori Business Social Compliance Initiative (BSCI). This means that the company not only commits itself to high social standards and sustainability, but also ensures compliance with social and labour law conditions by auditing its production partners.